Cassette system NOVA COMPOSITE
NOVA COMPOSITE is a prefabricated sandwich panel, with an LDPE core and covered on the outside with pre-weathered NedZink NOVA zinc. This combination creates a flat, stiff panel that is exceptionally suitable for use as façade cladding. Whether using glue, internal bracket cassettes, clamps or screws, there is a solution for every application. The panel is available in a standard thickness of 4 mm, for which the thickness of the NedZink NOVA top and bottom layer is 0.5 mm.
With NedZink NOVA COMPOSITE a façade can be created in zinc with large panel dimensions and exceptional flatness. Rounded elements and curved façades are possible. The assembly of the panel can be adjusted to the design.
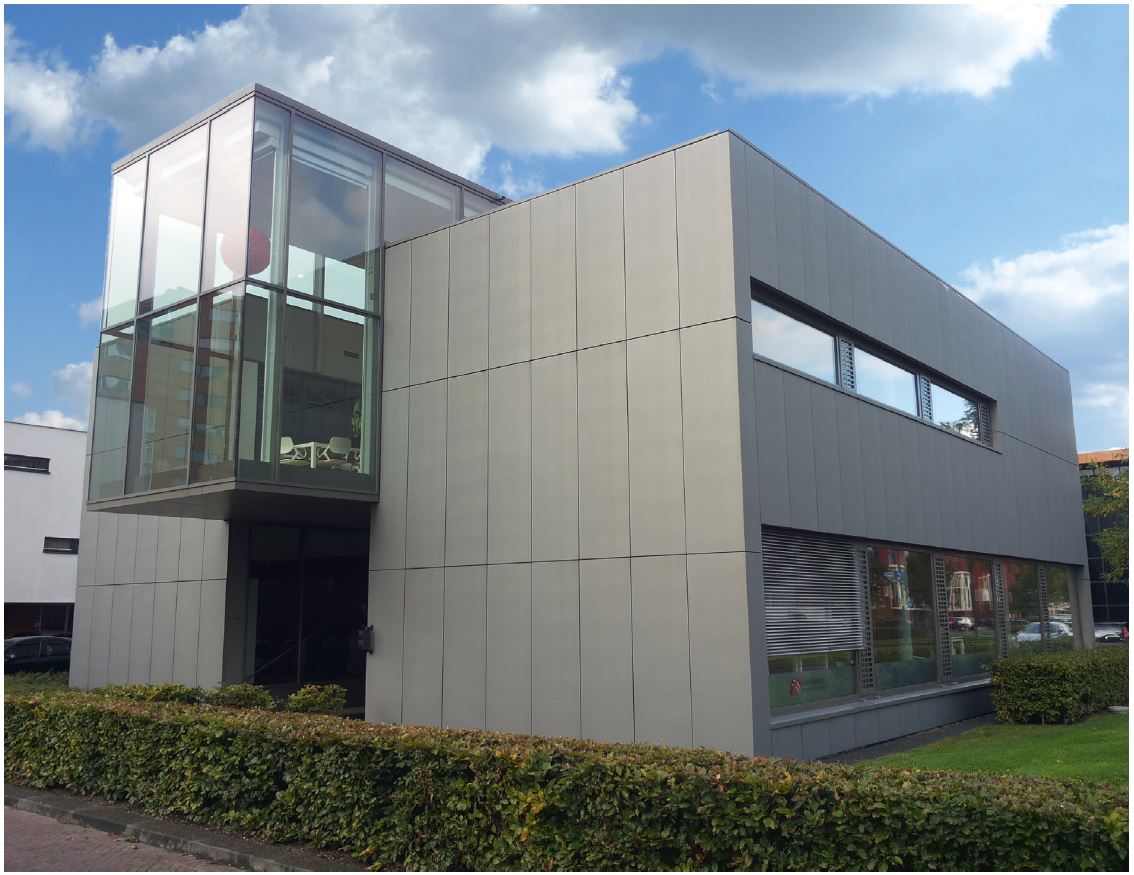
NOVA COMPOSITE is delivered as sheets on pallets. The material comes with a protective foil on the visible side as standard. The factory-applied anti-fingerprint coating protects the zinc against fingerprints during handling and assembly.

Product properties NOVA COMPOSITE | ||
---|---|---|
Standard dimensions* | 3200 x 1000 mm | |
Standard panel thickness | 4 mm | |
Panel composition | top and bottom layer: | 2 x 0,5 mm NedZink NOVA |
core: | 3 mm low density polyethylene (LDPE) | |
Toleranties | thickness: | -0 / +0,4 mm |
width: | + / -2,0 mm | |
length: | -0 / +4,0 mm | |
diagonal: | max. 3,0 mm |
*Other lenghts are available on request
Table 6.5.1
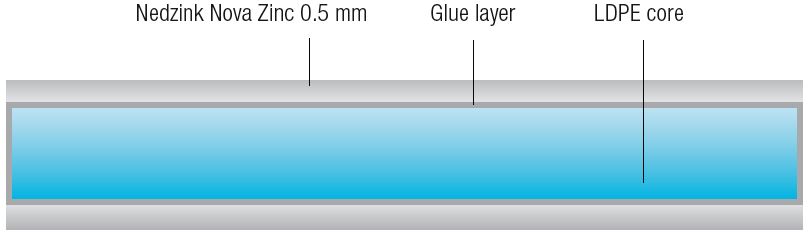
When processing it is always advisable to do a test to determine whether the requirements have been satisfied. The following techniques can be applied to NOVA COMPOSITE:
Sawing
The panels can be sawn with standard machines fitted with hardened bits. With standard bits, zinc causes accelerated wear of the cutting edges.
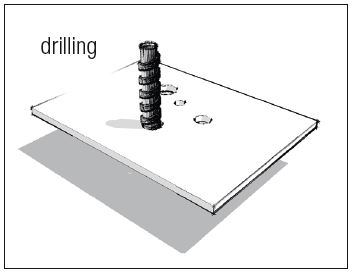
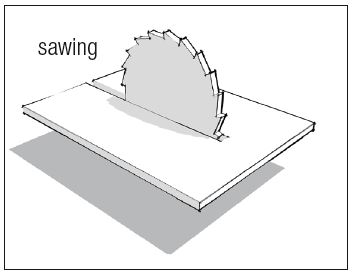
Shearing and perforating
The panels can be cut and punched with standard guillotine cutters and punch machines. Because NOVA COMPOSITE is built up of two metal layers and an LDPE core, a slight drawing of the zinc cover sheet caused by the impact side should be noted.
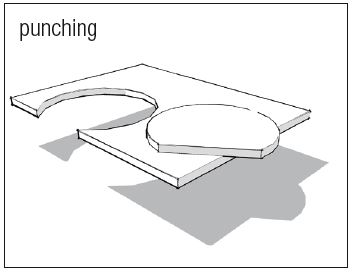
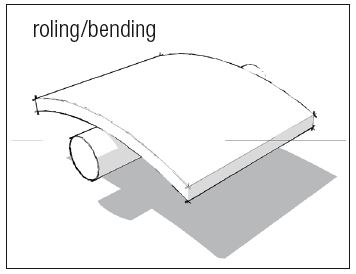
This can be an aesthetic choice. If a sharp cut is desired, start cutting or punching from the non-visible side. The minimum diameter of the perforation is 4 mm, minimum distance between and distance from the edge must also be 4 mm.
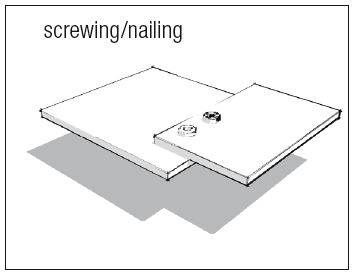
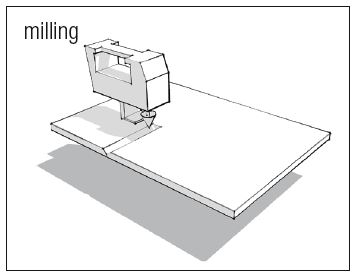
Milling and folding
NOVA COMPOSITE can be worked with specially hardened milling heads. Avoid scratches on the surface of the panel caused by loose cuttings and excessive pressure of the milling machine on the panel. It is important that at least 0.2 mm of the LDPE core remains. The panel can be bent after milling. The groove shape determines the radius of the bend. Never bend zinc under 7 °C; risk of cracks in the zinc surface.

Bending and rolling
The panel can be formed by conventional shaping tools and rollers. The minimum bend radius is 10x plate thickness. Before processing, a test piece should be made. The surface should be protected from damage by affixing plastic film strips during processing. The rolling direction is very important for the possible degree of warp of the panel. When bending in the longitudinal direction, tension in the metal is taken up less well, which can lead to the formation of cracks.
Screws
When screwing the panel in an exterior application it is important to maintain the waterproofing of the façade. For this, neoprene washers may be used with stainless steel top rings. The hole in the panel must be sufficiently large to take thermal movement of the panel into account. The screws must be set to the supported load and meet the set requirements. If the screws are screwed tight, the material can have insufficient movement and there is a chance of damaging the panel.
Attachment methods
The installation of the panel can be adjusted according to the design. The following attachment methods are possible with NOVA Composite:
• gluing
• clamping
• visible screws
• internal bracket system
When using the milling and folding technique the panel is given a special V groove, which makes it possible to bend the panel without special tools. Because of the remaining thin layer after milling, it is possible to fold the panel to the desired angle by hand or with hand tools. The groove shape determines the radius of the bend on the outside. When doing this, it is important that at least 0.2 mm of the LDPE core remains intact.
When processing it is always advisable to do a test to determine whether the requirements have been satisfied.